It is true that most of the people do not know the proper difference between all these wooden materials, thus it would lead to chosing the unsuitable material for your cabinet, your house or your project. Here are some of the comparison between MFC, MDF, HDF and PLYWOOD.
Industrial boards/ engineer boards are classified by wood core as follows:
• MDF: Medium Density Fiberboard
• HDF: High Density Fiberboard
• PLYWOOD
• MFC: Melamine Faced Chipboard
MDF (Medium Density Fiberboard)
MDF board is made from finely ground natural wood into fibers linked together by synthetic resin and compressed through pressure and heat. The board has a smooth surface, uniformed structure.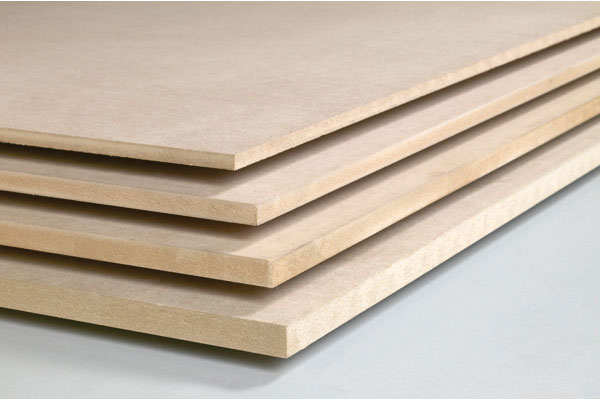
There are normal MDF, green-core moisture-proof MDF and sometimes even fire-resistant types that are now available in the market.
HDF (High Densiy Fiberboard)
HDF structure: using natural wood from planted forests as MDF, HDF is composed of 85% of finely ground natural wood, mixed with 15% of binders and additives (specialized glue) then pressed with strength, very high temperature and pressure. Therefore, HDF has better bearing and load capacity than MDF
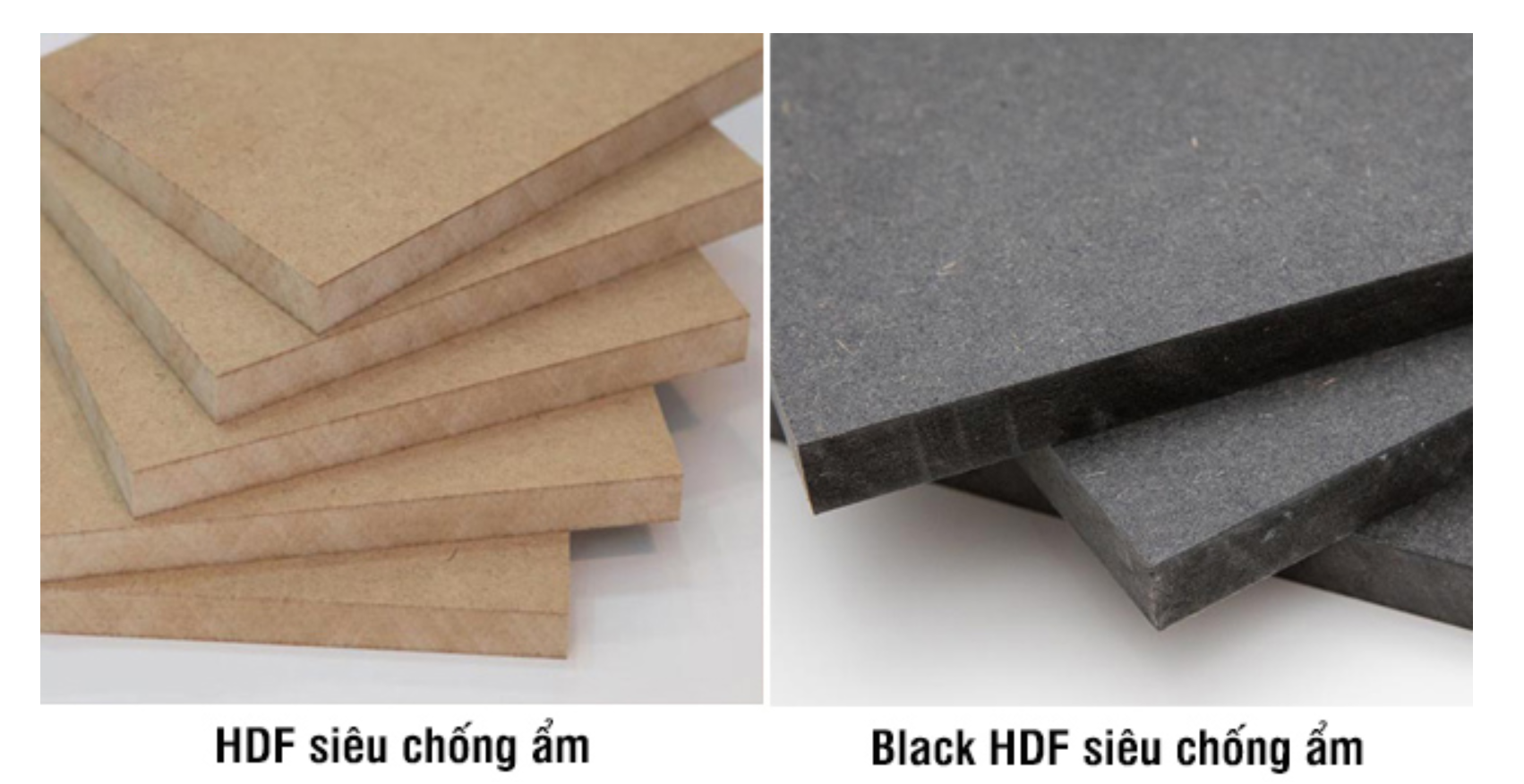
HDF properties: No shrinkage, no cracking, heat resistance, water resistance is relatively good. Smooth surface, heat and sound insulation.
Classification of HDF: Currently, the market has 3 main types: normal HDF, super moisture resistant HDF and super moisture resistant Black HDF.
PLYWOOD
Plywood is composed of many thin layers of wood with a thickness of approximately 1mm using specialized glue to press the layers perpendicularly. These thin layers of wood are peeled from natural wood, with high stability, very good bearing capacity.
Properties: Plywood does not shrink, does not crack, physical stability against warping, shrinking, and twisting of natural wood.
Plywood: has the following common thicknesses: 3,5,6,8,10,12,15,18,20,25 (mm)
Or you can contact to request the thickness according to your needs at HERE
MFC: Melamine Faced Chipboard
This is a natural wood that is ground into chips (not as fine as the wood pulp of MDF) then mixed with specialized glue and pressed with high pressure.
MFC has moderate bearing capacity, no shrinkage, poor moisture resistance; ordinary chipboard is prone to chipping at the edges. The ones that are resistant to moisture usually have a green core.
The surface of the board is rough, hence it is impossible to have veneer or laminate on its top.
COMPARISON OF MFC, MDF, HDF AND PLYWOOD
|
MFC
|
MDF
|
HDF
|
PLYWOOD
|
Strengh
|
The weakest matarial above these mentioned options
|
Stronger than MFC (particle board)
|
Stronger than MDF
|
1st place considered as the strongest material among all other option (just less stronger than solid wood)
|
Advantanges
|
-the cheapest option that you can get in the minimum budget
|
-Smooth surface, easy to glue or have veneer, laminate... on top
-Fast processing time
|
- Smooth surface, easy to glue or have veneer, laminate... on top
- Fast processing time
- Durable
|
- Has high durability, brightness, hardness
- No warping, shrinking, twisting
-Can be easily glued/ faced veneer, laminate... on its top
|
Moisture resistance
|
Very low, easy to get crumble when exposed to water for a long time.
|
Not high, easy to get crumble when exposed to water for a long time.
|
Higher than MDF
|
Highly moisture resistance. Especially suitable for hot and humid tropical climate places.
|
Lifespan
|
Less than 2 years
|
About 2-5 years
|
About 4-7 years
|
More than 15 years
|
Cost of material
|
cheap
|
Normal
|
Higher than MDF
|
Higher than HDF
|
Usage
|
- Pallet
|
- Construction furniture
|
- Construction furniture
- Cabinets and shelves for storage.
|
- Kitchen furniture and cabinets for kitchen and bathroom.
|
The above is the information about the types of industrial wood planks; hope you can make the proper choice according to your needs and requirements for any furniture or construction projects.
You can refer to more popular veneer models at:https://veneerbmt.com/san-pham/veneer for more interior ideas.